En 2016, plus de 170 pays ont signé l’accord de Paris, s’engageant à freiner le réchauffement climatique et les émissions de carbone. L’objectif était de limiter l’augmentation de la température moyenne mondiale à moins de 2°C au-dessus des niveaux préindustriels. Actuellement, plus de 90 pays dans le monde se sont fixés des objectifs pour atteindre 50% de la production totale d’électricité à partir d’énergies vertes d’ici 2025, avec plus de 50 nations envisageant d’atteindre 100% d’énergies vertes d’ici 2050.
La réserve d’énergie éolienne terrestre théorique disponible pour le développement et l’utilisation est d’environ 2,53 milliards de kilowatts, tandis que la réserve éolienne offshore est d’environ 7,5 milliards de kilowatts, totalisant environ 10 milliards de kilowatts. Depuis 2016, le marché de la maintenance de la production d’énergie éolienne est en forte croissance.
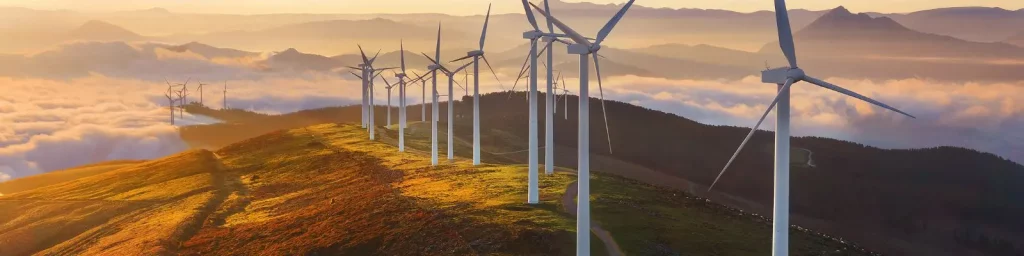
La capacité d’une éolienne à atteindre des performances optimales pendant sa période de fonctionnement est un facteur crucial pour évaluer le succès ou l’échec de l’investissement dans ce type d’énergie. Pour s’en assurer il est important d’assurer la maintenance opérationnelle de ces équipements durant l’ensemble du cycle de vie : fabrication, l’installation à la mise hors service finale. A savoir qu’on parle ici d’une durée de vie d’environ 20 à 25 ans.
Un des points critiques sont les pales. Elles sont en extérieur et font face à de nombreux défis pour les maintenir :
- Les méthodes traditionnelles de surveillance manuelle sont difficiles, coûteuses et impliquent un temps d’arrêt prolongé de la turbine. Elle sont uniquement adaptées pour détecter les fissures des pales et les impacts de foudre.
- La méthode consistant à intégrer des capteurs dans les pales pour une surveillance en temps réel sans temps d’arrêt, est difficile et coûteuse.
- Bien que l’utilisation de véhicules aériens sans pilote (UAV) ou drones pour l’inspection des pales soit rentable, la turbine doit être arrêtée et une surveillance en temps réel n’est donc pas possible.
L’inspection visuelle par IA pour réduire les coûts de maintenance
Certains fournisseurs de solutions pour éoliennes proposent d’intégrer un système d’inspection visuelle par intelligence artificielle dans une exploitation et une maintenance globale et intelligente de parcs éoliens.
Ce type de solutions offrent des avantages tels que de faibles coûts d’investissement, la capacité de réaliser une surveillance en temps réel sans temps d’arrêt, une large couverture de détection et une haute précision. Cette approche est la plus efficace pour prévenir de manière proactive les dommages aux éoliennes et maximiser la production d’énergie en surveillant l’état des turbines en temps réel.
Par exemple, certains intégrateurs sur le marché chinois, ont développé des modèles d’IA entraînés sur des données réels. Ces derniers permettent par exemple de détecter les points suivants :
- Détection de l’accumulation de glace
- Détection de fissures
- Reconnaissance des impacts de foudre
Bien sûr, une fois un problème détecté, un avertissement est généré pour une intervention rapide.
Ce type de solutions est compact et basé sur un système composé d’un PC d’inférence IA et de caméras. Il est installé directement dans l’éolienne. Aucun temps d’arrêt n’est nécessaire pour sa mie en place.
Avec notre partenaire Advantech plusieurs solutions, basée sur l’architecture NVIDIA Jetson, peuvent répondre à ce type de besoin :
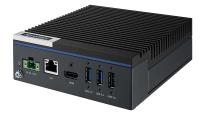
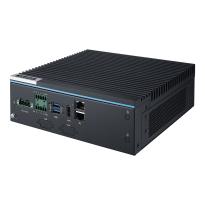
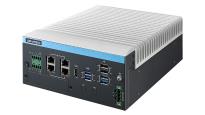
Bien sûr les modèles peuvent être adapté aux spécificités de chaque parc. Ce type de solution de maintenance diminue les temps d’arrêts, améliore les performances, augmente la production d’énergie et prolonge la durée de vie des turbines.
Principaux avantages de l’IA pour la maintenance des éoliennes
- Fonctionne sur un parc éolien installé : Il est possible de faire de la maintenance sans remplacer l’ensemble du système. Aucun temps d’arrêt de la turbine n’est requis.
- Surveillance par image : Utilisation de caméras pour une surveillance en temps réel. Des contrôles visuels des conditions peuvent être donc réalisés par des utilisateurs si le système est connecté.
- Détection de défauts en temps réel : Les données sont envoyés aux modèles d’inférence qui permet une détection instantanée des défauts des pales en fonctionnement. Ils émettent si nécessaire des alarmes.