L’avènement de l’inférence dans le secteur industriel marque une ère où les machines ne se contentent plus d’exécuter mais apportent également de l’intelligence temps réel sur le terrain. Cette intégration, notamment via l’apprentissage automatique (machine learning) et l’intelligence artificielle (IA), révolutionne les processus de fabrication, la maintenance industrielle et la gestion de la chaîne logistique. L’inférence c’est la capacité à tirer de nouvelles informations à partir de modèles préalablement entraînés sur des données. Aujourd’hui elle devient un levier de performance et d’innovation pour l’ensemble du secteur industriel.
L’inférence, dans le domaine de l’intelligence artificielle, est le processus par lequel un modèle pré-entraîné utilise des données en usage réel pour faire des prédictions ou prendre des décisions.
Quand la machine devient prédictive avec l’inférence
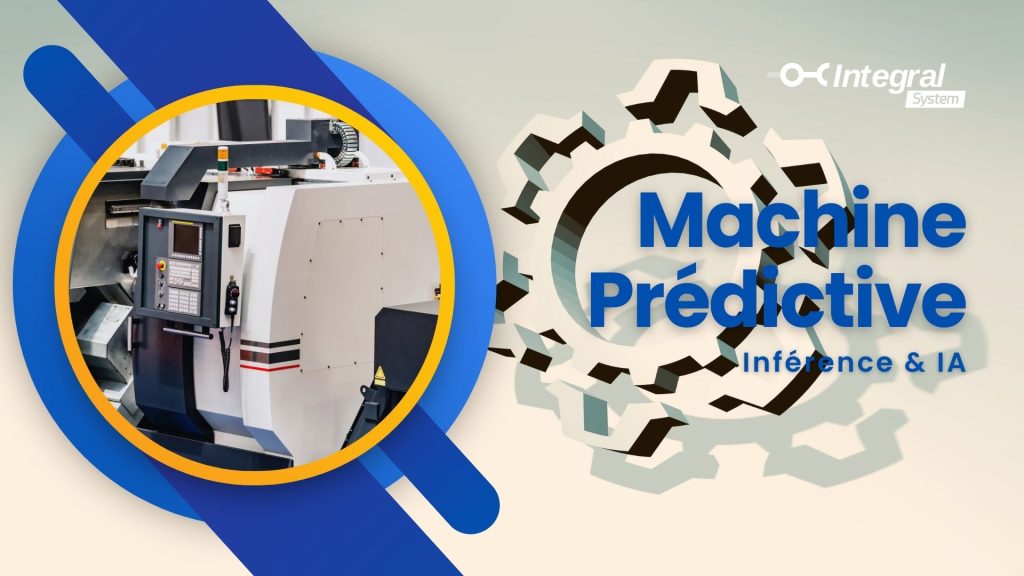
L’inférence au sein des domaines industriels permet aux machines et systèmes de production de prédire des comportements, des pannes ou des anomalies avant même qu’ils ne surviennent. Grâce à des algorithmes sophistiqués et à des capteurs disposés sur les équipements, les données récoltées en temps réel servent à alimenter des modèles d’IA qui, par la suite, optimisent les décisions et les actions entreprises.
Optimisation des Chaînes de Production avec l’Inférence
L’inférence contribue significativement à l’optimisation des chaînes de production. Ces systèmes sont capables d’analyser rapidement de grands volumes d’informations et de suggérer des ajustements pour améliorer l’efficacité. C’est, par exemple, un des cas d’usages du jumeau numérique, en développant une reproduction d’un processus de production, il est possible d’inclure l’organisation de l’ordre des tâches, la gestion des flux de matériaux ou l’adaptation des paramètres et processus de production. L’avantage de ces simulations, c’est de pouvoir agir sur des centaines de variables, pilotées par l’IA, pour analyser des scenarii réels.
- En intégrant l’ERP, la CRM et les outils de logistique il est possible de faire de la prévision de demande et gestion des stocks
- En intégrant l’IIoT, les outils de maintenance et l’IA il est possible de faire de la maintenance préventive
- Optimisation des processus de production en temps réel grâce à la prédiction et l’analyse de gigantesques volumes de données.
L’analyse de données, un rôle clef
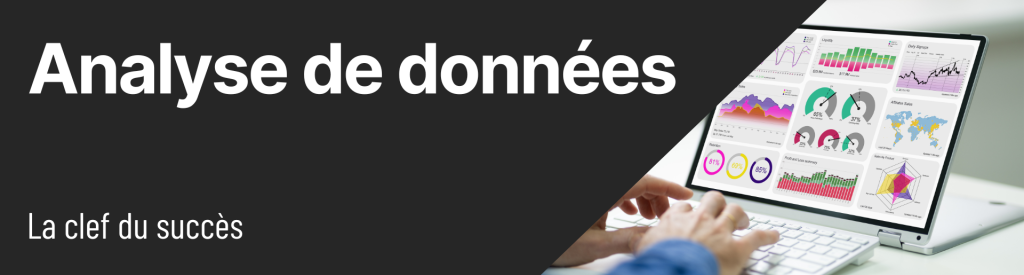
La transition vers l’industrie 4.0 repose entre autre sur la capacité à extraire, analyser et exploiter les données. L’inférence est une brique essentielle à cette transition. Elle permet d’extraire des connaissances et de la valeur à partir de la masse de données générée par les capteurs industriels et l’ensemble des systèmes de l’usine. L’analyse prédictive est notamment utilisée pour anticiper les défaillances et optimiser l’utilisation des ressources.
La maintenance directement impactée
La maintenance prédictive se base sur les principes d’inférence pour prévoir quand et où des actions de maintenance seront nécessaires. Elle peut se matérialiser de différentes manières, que ce soit directement au sein d’un capteur intelligent, ou d’un mini PC optimisé pour. Ceci minimise les arrêts imprévus et prolonge la durée de vie des équipements.
Exemples d’applications de l’inférence
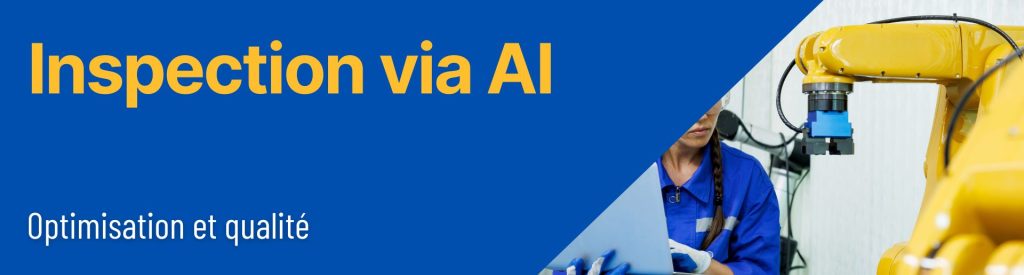
L’inférence se manifeste à travers diverses applications concrètes dans l’industrie. Les systèmes d’inspection visuelle automatisés utilisent de plus en plus cette technologie pour détecter les défauts de fabrication. Les robots autonomes s’orientent et s’adaptent à leur environnement pour effectuer des tâches complexes sans intervention humaine. Et les plateformes de gestion de la chaîne logistique en tirent partie pour optimiser le transport, les flux logistiques, la distribution et l’inventaire.
De nos jours, cette technologie d’IA, joue un rôle fondamental dans la 4ème et 5ème révolution industrielle. Elle permet aux entreprises industrielles de réagir de plus en plus en avance de phase vis à vis des défis complexes. Les nombreux progrès en IA et en analyse de données (LLM, ChatGPT, Google Gemini, …) ouvrent la porte à des améliorations en termes d’usages, de compréhension des systèmes, de qualité, d’efficacité et de durabilité des opérations industrielles.
Amélioration des chaînes de production grâce à l’inférence
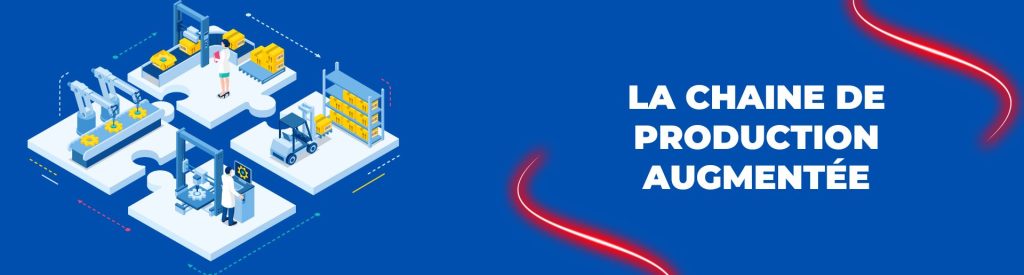
L’inférence dans les chaînes de production industrielles n’est pas une nouvelle tendance, mais une suite logique à l’amélioration continue des processus.
En analysant les gigantesques volumes de données, elle permet de détecter et d’anticiper les événements au sein de la production pour générer une réaction en temps réel. Par exemple, en captant les signaux faibles (pattern) à travers les données récoltées, les algorithmes d’IA permettent de prédire des pannes, des ralentissements ou des défauts de qualité avant qu’ils ne se produisent, et de prescrire les actions correctives nécessaires.
Elle contribue à l’augmentation de l’efficacité des chaînes de production, à la réduction des coûts et à l’amélioration de la qualité des produits finaux.
Amélioration de l’efficacité opérationnelle
En analysant les données de la chaîne de production, l’inférence peut aider à déterminer les goulots d’étranglement et à identifier les étapes qui peuvent être optimisées. Par exemple, si une machine en particulier cause des retards ou des problèmes de qualité, ce type de système peut indiquer si elle nécessite une maintenance préventive ou un remplacement.
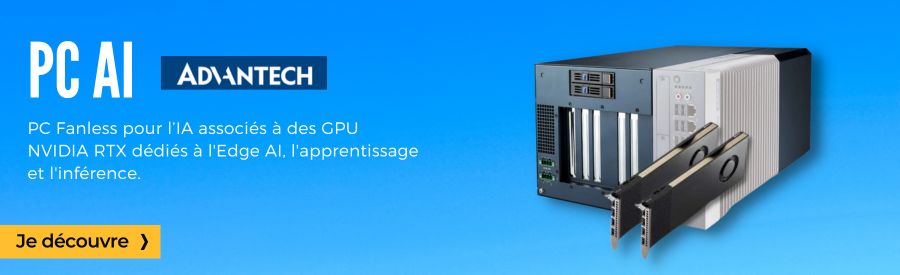
Des critères d’efficacité opérationnelle incluent:
- La réduction des temps d’arrêt
- L’amélioration du taux de rendement synthétique (TRS)
- La diminution des cycles de production
- La gestion optimisée des ressources
Une des forces de l’inférence réside dans l’apprentissage machine en continue. Elle évolue et s’améliore avec le temps. Plus le système récolte d’informations, plus ses prédictions deviennent précises, permettant la mise en place de processus d’améliorations continues encore plus précis et pertinents.
Valorisation des données et des outils analytiques
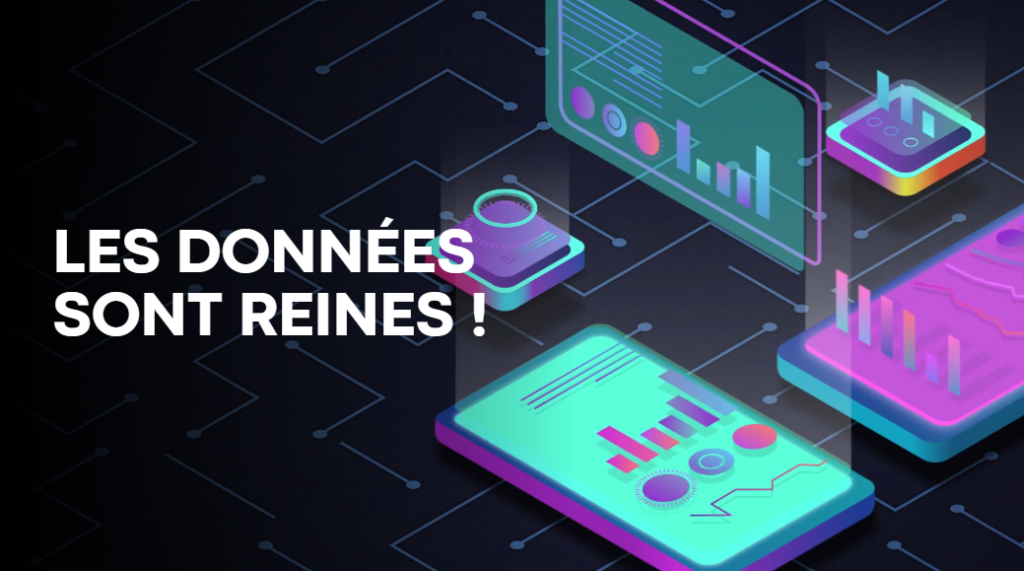
L’inférence repose sur une collecte et une analyse de données. Les outils analytiques jouent un rôle clé dans l’extraction du sens et de la valeur de ces données et nécessitent un investissement en matériel et logiciel, ainsi qu’en formation du personnel.
De nombreuses marques (Siemens, IBM, OpenAI, Advantech, NVIDIA) commencent à proposer des systèmes d’inférence et d’analyse de données pour l’optimisation de la production.
Impact environnemental réduit
L’inférence contribue à un environnement de production plus durable en optimisant la consommation d’énergie et en réduisant les déchets, s’alignant ainsi sur les pratiques d’éco-efficience et les objectifs de développement durable. A ce jour on notera particulièrement 3 axes de travail :
- Diminution de l’empreinte carbone
- Optimisation de l’utilisation des ressources disponibles
- Réduction des déchets
En exploitant les dernières avancées dans le domaine de l’intelligence artificielle et de l’analyse de données, elle ouvre la porte à des processus de production plus efficaces, réactifs et durables.
La maintenance prédictive, un tournant pour la fiabilité
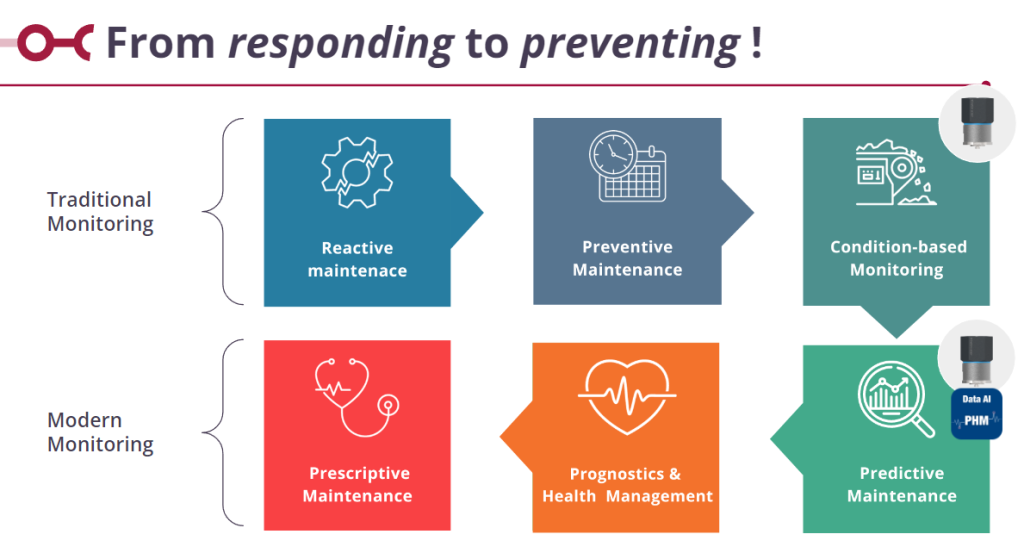
L’inférence et la maintenance prédictive est un nouveau duo impactant dans le domaine de la gestion d’équipements industriels. Leur convergence transforme notre manière d’aborder la fiabilité des machines. Au lieu de répondre aux interruptions imprévues, on les anticipes. Ce phénomène génère une réduction drastique des coûts associé à l’arrêt machine.
Le principe de l’IA en maintenance industrielle
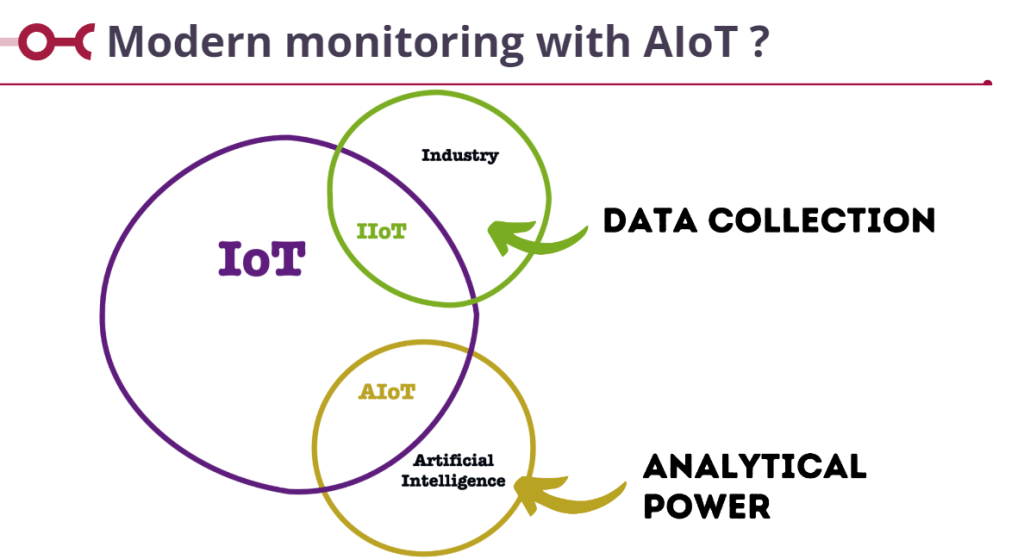
Dans le contexte industriel, l’IA utilise des données et des statistiques pour tirer des conclusions sur l’état d’un équipement ou d’un système. Grâce à des algorithmes avancés, du machine learning, au deep learning, en passant par les LLM (Large Model Language) les solutions d’IA peuvent analyser des quantités massives de données pour détecter des tendances, des anomalies et prédire les défaillances futures des équipements. Le tout est bien souvent rapporté à des données connues des standards définis et reconnus du marché.
Les avantages :
- Analyse des données de fonctionnement en temps réel
- Détection des écarts par rapport aux modèles de performance attendue
- Identification des signes avant-coureurs de panne
Aujourd’hui pour implémenter ce type de solution, les systèmes continues à se baser sur la remontée de données du terrain, l’utilisation de ressources informatiques et l’intervention humaine :
- Utilisation de capteurs IoT pour la collecte de données
- Intégration de systèmes d’IA pour l’analyse prédictive
- Planification des interventions avant l’occurrence des défaillances
Grâce à des logiciels tels que IBM Maximo, SAP Predictive Maintenance and Service ou encore Advantech WISE-IoT/PHM il existe des solutions métiers capables de prédire les besoins de maintenance avec précision. D’ailleurs Integral System parlait de l’AIoT en Octobre 2023 durant la World Partner Conference chez Advantech.
La donnée IoT au coeur de ce processus
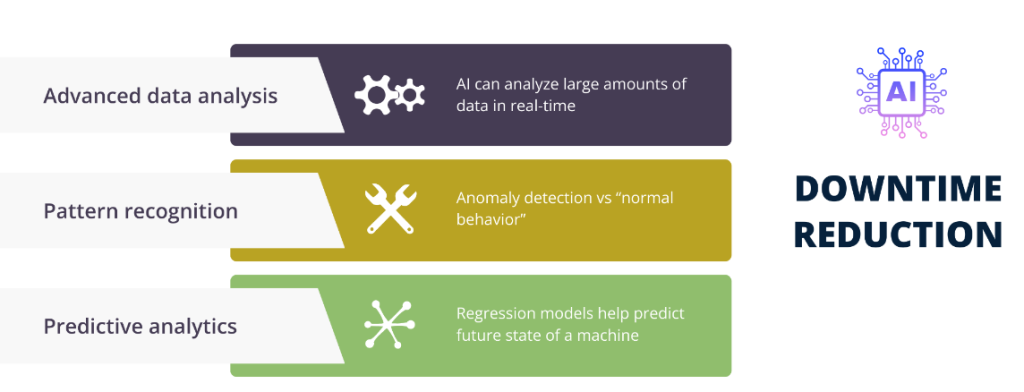
La qualité et la quantité des données est cruciale pour assurer la pertinence de la maintenance prédictive. Les capteurs doivent être sélectionnés et placés pour capter l’information la plus importante. C’est pourquoi il est crucial de faire un pré-traitement des données dans l’Edge afin de filtrer du bruit inutile.
Ci-dessous quelques exemples d’utilisations :
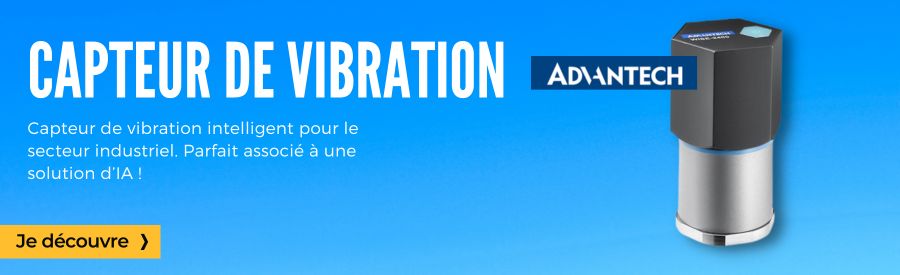
Type de Capteur | Données Récoltées | Utilisation |
Capteur de vibrations | Fréquences des oscillations | Détection des anomalies moteur |
Capteur de température | Dégrées Celsius ou Fahrenheit | Surveillance des surchauffes |
Capteur de Pression | Bars ou Pascal | Évaluation de la performance des systèmes hydrauliques |
Capteur de courant | Ampères | Surveillance de la consommation électrique |
Malgré ses avantages, la mise en œuvre d’un système de maintenance prédictive s’accompagne de défis, notamment en termes de compétences techniques nécessaires pour interpréter les données.
Les entreprises doivent dès à présent, investir dans la formation de leur personnel ou s’appuyer sur des partenaires spécialisés.
La protection des données et la cybersécurité deviennent des préoccupations majeures à l’heure où les usines sont de plus en plus connectées. Elles doivent être prise en compte dès l’initiation de toute projet IoT.
La personnalisation et l’innovation produit
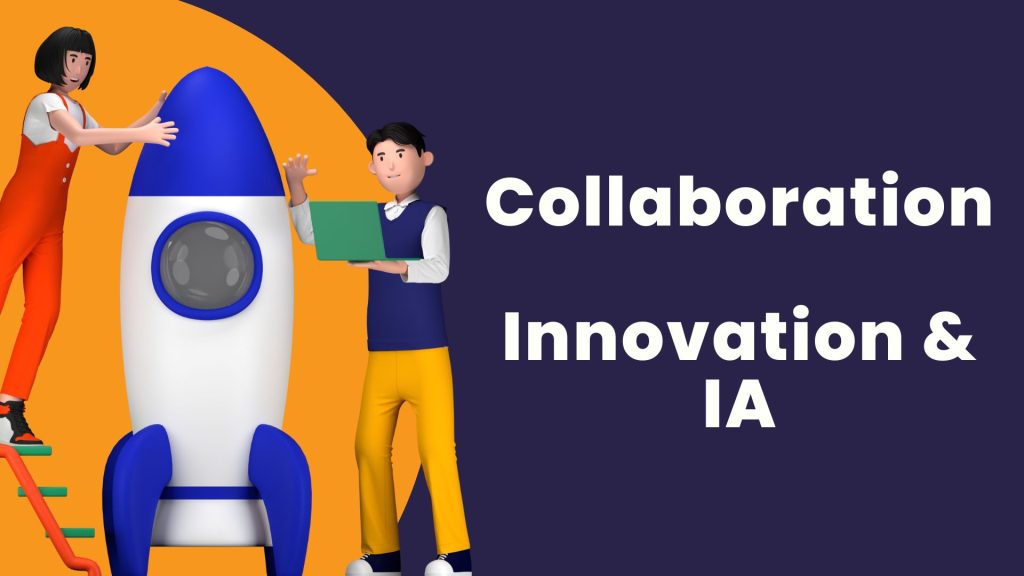
Vous l’aurez compris, l’industrie moderne est en pleine révolution, notamment avec les technologies de l’intelligence artificielle, l’IoT et du big data. Les systèmes d’inférence automatisés basées sur l’IA, deviennent des acteurs majeurs dans la personnalisation de masse et l’innovation produit.
C’est en croisant plusieurs sources de données et en utilisant la puissance d’un système d’IA entrainé, que les entreprises peuvent concevoir des produits adaptés aux besoins individuels de chaque client, tout en maintenant des coûts et des délais de production optimisés.
Personnalisation de masse
La personnalisation de masse, ou customisation de masse, associe production en volume et personnalisation pour offrir des produits adaptés aux préférences spécifiques de ses clients.
L’inférence, dans ce contexte, tire parti des données clients pour anticiper leurs demandes et ajuster en conséquence la production. Voici un exemple de processus de personnalisation :
- Compréhension du client : Les algorithmes collectent et analysent les habitudes de consommation (CRM), les interactions en ligne (réseaux sociaux) et les retours clients pour cerner avec précision leurs besoins.
- Prédiction des tendances : En analysant les tendances à partir du comportement passé et actuel des clients, les entreprises adaptent leur offre pour devancer la demande.
- Optimisation de la production : La production peut être ajustée en temps réel pour répondre à des commandes personnalisées sans gaspillage de temps ou de ressources.
Innovation produit
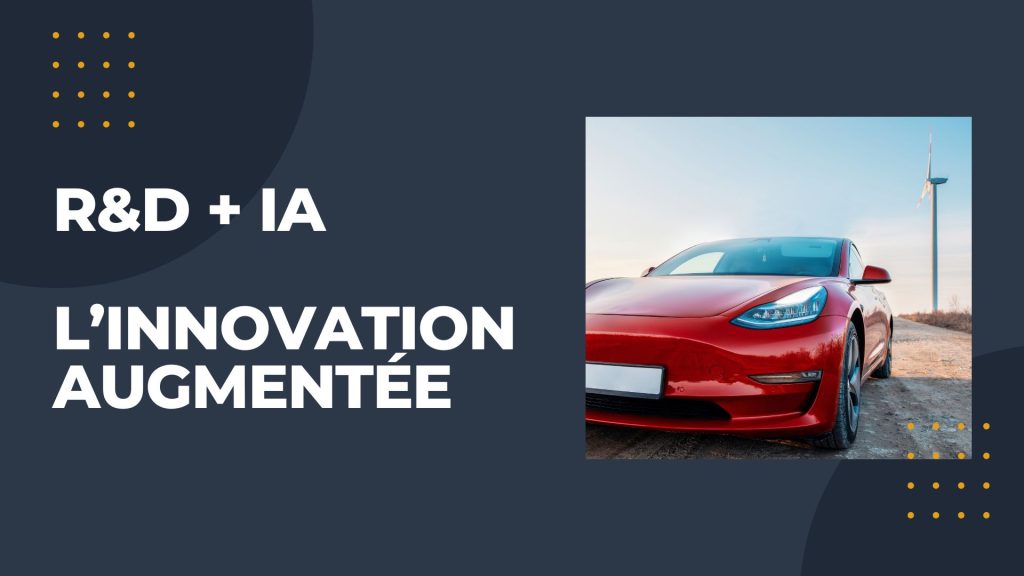
Le développement de nouveaux produits est un défi constamment relevé par les industries du monde. L’intelligence artificielle peut rendre ce processus plus performant encore, en offrant des idées basés sur une grande quantité de données. Des sociétés comme Google, Amazon, Microsoft ou Tesla exploitent les données pour concevoir des innovations qui répondent très précisément aux attentes de leurs clients.
- Analyse prédictive : Elle permet d’identifier quels pourraient être les futurs besoins des utilisateurs ou les problèmes encore non résolus.
- Détection de motifs : L’identification de patterns au sein des données aide à trouver de nouveaux usages pour des produits existants ou à créer des produits totalement nouveaux.
- Réduction des cycles de développement : En fournissant rapidement des informations essentielles, l’inférence raccourcit le temps de recherche et développement.
- Analyse en temps réel des réactions des clients pour itération
La collaboration entre l’humain et les systèmes d’IA est cruciale pour l’innovation
En effet, les idées provenant de ce type de systèmes ne peuvent être utilisées efficacement que lorsqu’ils sont intégrés dans un processus d’innovation collaboratif avec les concepteurs et les ingénieurs. D’ailleurs il devient de plus en plus commun d’utiliser les termes « Augmenter par l’IA » que remplacé par l’IA.
Aujourd’hui avec les systèmes comme Dall-E, MidJourney, Adobe Sensei ou Adobe Firefly, il existe déjà une cocréation réelle entre l’IA et les designers. En allant plus loin et en imaginant des jumeaux numériques, il est même possible de tester virtuellement des variantes, ainsi que leurs performances, avant d’aller vers le prototype physique.
On remarque que l’IA apporte sa pierre à l’édifice dans nombre d’aspects de l’industrie. Elle permet une diminution des coûts, une augmentation de l’agilité et une mise en place d’un processus d’innovation constant par la connaissance client.